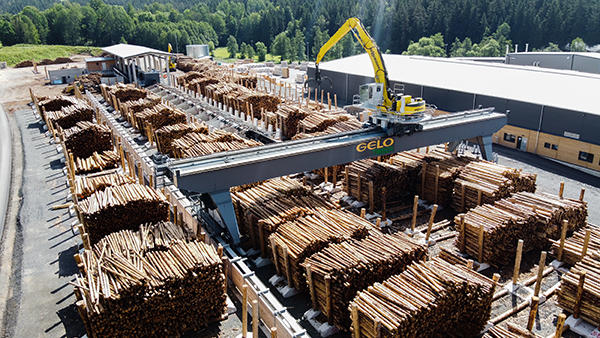
Sfruttare al meglio le risorse naturali disponibili in loco e integrarle le une alle altre – questo è uno dei principi guida del parco energetico di Wunsiedel. La WUN Bioenergie è una joint venture della SWW Wunsiedel GmbH e della GELO Holzwerke di Weißenstadt. La GELO utilizza il legno presente in abbondanza sul Fichtelgebirge per produrre soprattutto pannelli in legno per l’edilizia e travi in legno massiccio da costruzione. I residui vengono trasformati in pellet nel parco energetico o conferiti in una grande centrale di cogenerazione a biomassa. Per preparare i resti di legno per questi impieghi, il gestore fa affidamento sull’efficiente tecnologia di triturazione e trasporto di Vecoplan.
«Tra il 2008 e il 2018, il settore delle segherie ha subito una concorrenza spietata con una forte pressione sui prezzi», riferisce Wolf-Christian Küspert, titolare e direttore generale della GELO Holzwerke di Weißenstadt, in Alta Franconia. «Ben il 30 percento delle aziende è sparito dal mercato, e quelle che sono riuscite a sopravvivere hanno dovuto fare fronte a ingenti perdite. Di conseguenza, nel settore si è accumulato un enorme ritardo negli investimenti che ora si sta progressivamente risolvendo.» Küspert ha rilevato l’azienda di famiglia da suo padre nel 2003. Con circa 600’000 metri cubi di legno tagliato all’anno, l’azienda, fondata nel 1898 come segheria, è oggi uno dei maggiori gruppi di lavorazione del legno in Germania – e sorge in un’area industriale altamente avanzata a Weißenstadt. «Grazie alla nostra capacità di eseguire diverse operazioni di finitura in loco, da noi i clienti trovano tutto da un unico fornitore», afferma il direttore generale.
Nel 2011 l’azienda, insieme alla Stadtwerke Wunsiedel (SWW), ha fondato la WUN Bioenergie GmbH di Wunsiedel. Grazie a una centrale di cogenerazione a biomassa ubicata in un’area vicina, la filiale produce energia da fonti rinnovabili e soprattutto di provenienza regionale. Alla GELO non vengono pertanto prodotti rifiuti, poiché gli alberi vengono totalmente recuperati: per esempio, il cippato derivante dalla produzione viene conferito nell’industria della cellulosa. I trucioli vengono pressati per produrre pellet utilizzati per generare energia e calore sostenibile nelle abitazioni della regione.
«Abbiamo ampliato più volte la sede di Weißenstadt», riferisce Küspert. A un certo punto, tuttavia, abbiamo dovuto fermarci. Eravamo al limite delle nostre disponibilità di spazio.»
Per poter crescere ancora, l’unica strategia logica era rivolgere lo sguardo altrove: nella città di Wunsiedel, a pochi chilometri di distanza, il nuovo parco energetico ospitava già una centrale di cogenerazione e una fabbrica di pellet. Qui, l’azienda di lavorazione del legno ha costruito la segheria GELO Timber – uno dei pochi progetti greenfield realizzati in questo settore in Germania negli ultimi anni.
Nell’aria c’è odore di legno appena tagliato. Wolf-Christian Küspert indica il nuovo capannone. «Qui abbiamo costruito la segheria per legname di piccole dimensioni più avanzata a livello mondiale», afferma. Il legname di piccole dimensioni è un legno di qualità particolarmente elevata, con nodi di crescita aderenti. Con quest’attività, l’azienda sostiene anche la crescente attività di conversione e ripristino delle foreste. A causa del cambiamento climatico, infatti, gli alberi più vecchi muoiono prima e quelli in crescita devono essere abbattuti anzitempo. «Il legno ha un diametro in punta di circa 25 centimetri o inferiore», spiega Küspert. «Dal legname di piccole dimensioni derivano sempre anche molti resti di legno. Questo perché, quanto minore è il diametro, tanto più elevata è la quantità di resti di legno che produciamo per ricavare una sezione rettangolare.» Lo stabilimento di Wunsiedel lavora perlopiù legno di abete rosso – ben 350’000 metri cubi all’anno.
Trattamento efficiente dei resti di legno
Per trattare la segatura e il cippato per la produzione di pellet, la GELO Timber ha puntato su Vecoplan – come già da anni faceva a Weißenstadt. Lo specialista del trattamento di materiali residui, con sede principale a Bad Marienberg (Westerwald), sviluppa impianti per triturare, convogliare, separare e stoccare legno, biomassa, materie plastiche, carta, nonché rifiuti domestici e commerciali. «I nostri compiti comprendono servizi come la consulenza, la pianificazione con conseguente ricerca di soluzioni, la gestione globale del progetto, nonché il montaggio, la messa in servizio e l’assistenza completa» spiega Michael Mützel, Area Sales Manager Wood I Biomass di Vecoplan. Wolf-Christian Küspert lo conosce da tempo grazie alla collaborazione a progetti comuni. Da ancor più tempo, il direttore generale conosce Vecoplan: «Già mio padre e mio nonno avevano puntato sull’affidabilità delle macchine e sulla competenza dell’azienda. Sono quindi letteralmente cresciuto con questo nome. Posso solo dire: a ciascuno il suo mestiere.»
Vecoplan ha preso parte al progetto sin dall’inizio. «A gennaio 2020 abbiamo ricevuto la commessa», racconta Michael Mützel. «Abbiamo fornito assistenza durante la progettazione e abbiamo potuto realizzare i nostri impianti completamente ex novo.» La consegna è avvenuta nell’estate 2020, il montaggio e la messa in servizio a novembre.
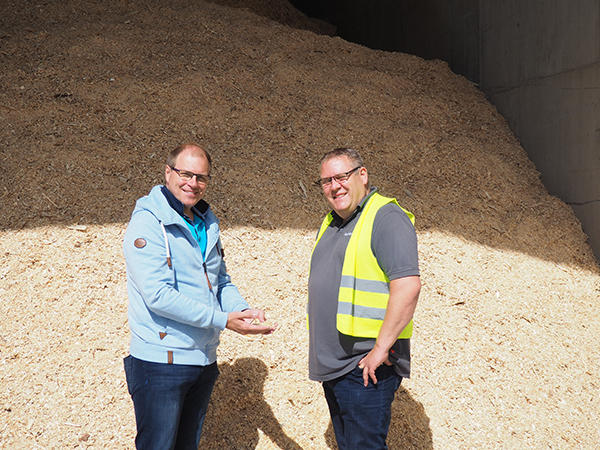
Produzione di legname di piccole dimensioni
Il rumore delle macchine riempie il capannone. Mützel, esperto Vecoplan, mostra gli impianti installati dal team dell’azienda. Dalla linea di taglio, la segatura e il cippato cadono su un lungo nastro trasportatore che si snoda sul pavimento del capannone. Per separare i pezzi troppo lunghi, il sistema di trasporto convoglia il materiale verso un vaglio a stella. I resti di legno di dimensioni adatte cadono su un altro nastro trasportatore. I pezzi troppo lunghi filtrati dal vaglio e i ceppi derivanti dalla separazione dei pannelli vengono invece convogliati al tamburo cippatore attraverso nastri e vibri trasportatori. Questi ultimi trasportano il materiale da lavorare nella macchina in senso orizzontale. Per ottenere un prodotto finale omogeneo e di elevata qualità, i tecnici Vecoplan hanno adattato il cippatore alle esigenze di produzione della segheria.
«La nostra serie è estremamente compatta», afferma Mützel. «Il principio di triturazione fa sì che i resti di legno vengano triturati a una lunghezza di circa dieci millimetri, in modo da poter essere convogliati direttamente al processo di essiccazione nello stabilimento di produzione di pellet antistante.»
Il cippato prodotto dal trituratore viene poi nuovamente riversato sul lungo nastro trasportatore sotto la linea di taglio. Un trasportatore a catena unisce i resti di legno ripuliti dai pezzi troppo lunghi con il materiale passato attraverso il vaglio a stella e proveniente dal capannone e trasferisce il tutto su un trasportatore a nastro tubolare VRF lungo 40 metri che lo convoglia allo stabilimento di produzione di pellet.
Nulla deve andare perduto
«Rispetto a sistemi a nastri trasportatori equivalenti, questa serie consuma la metà di energia elettrica», afferma Mützel. Il VRF trasporta il materiale percorrendo diagonalmente l’area esterna fino ai contenitori di stoccaggio e a una postazione di vagliatura. Affinché nulla vada perduto, l’impianto tubolare racchiude completamente il materiale al suo interno evitando così che possa essere soffiato via da temporali o vento. Il nastro trasportatore di questa serie passa attraverso un tubo e non su rulli, come avviene nei comuni impianti trasportatori. Poiché il nastro poggia su un cuscino d’aria, le perdite per attrito dovute al movimento sono molto ridotte. Di conseguenza, l’impianto risulta silenzioso contribuendo a creare un clima più gradevole nell’area di produzione.
Ogni unità di azionamento è dotata di due raschiatori. L’utente può regolare il pre-raschiatore e il raschiatore in metallo duro dall’esterno. Il serraggio dei componenti può essere corretto a posteriori facilmente e in poco tempo utilizzando un cricchetto. Il pre-raschiatore è flessibile, ma sufficientemente stabile per rimuovere le impurità dal nastro. Il raschiatore in metallo duro agisce più a fondo e impedisce che sul nastro trasportatore possano ad esempio rimanere particelle di resina. Questi raschiatori riducono la necessità di manutenzione, aumentano la disponibilità degli impianti e limitano la propagazione di materiale. L’impianto trasporta il materiale a una velocità massima di 2,5 metri al secondo. Dalla postazione di vagliatura, un altro trasportatore Vecobelt lungo 80 metri convoglia infine i resti di legno allo stabilimento di produzione di pellet.
Un’ubicazione ottimale
«Qui, le distanze di trasporto sono brevi e a basso consumo energetico. La vicinanza tra i vari impianti ci permette di risparmiare ogni anno alcune migliaia di viaggi in camion», afferma Küspert. I pellet non vengono venduti solo a livello regionale, ma vanno anche ad alimentare diversi impianti a gassificazione a pellet in uso presso la società di servizi energetici Stadtwerke Wunsiedel, la GELO e altri partner. La corrente prodotta viene immessa nella rete SWW. Il calore alimenta le reti di teleriscaldamento dei quartieri adiacenti. Inoltre, il calore residuo derivante dalla centrale elettrica viene utilizzato per l’essiccazione dei trucioli nello stabilimento di produzione di pellet.
«Un progetto così grande può riuscire solo se ci si affida ai partner giusti», afferma convinto Küspert. «Per ridurre la complessità, devo poter fare affidamento su di loro. Con un partner come Vecoplan, so che andrà tutto liscio. E se dovessero esserci criticità, gli specialisti sanno esattamente dove intervenire.» Il progetto prevedeva tempi di realizzazione piuttosto serrati. A questo si è aggiunta la pandemia. Le restrizioni ai viaggi hanno causato ritardi nei lavori dei montatori provenienti dalla Finlandia o dal Portogallo. A fine febbraio 2021, l’azienda di lavorazione del legno ha finalmente iniziato a lavorare a regime. Solo tre mesi più tardi, l’azienda aveva già raggiunto un livello di produzione costante, pari all’80 percento della capacità massima.