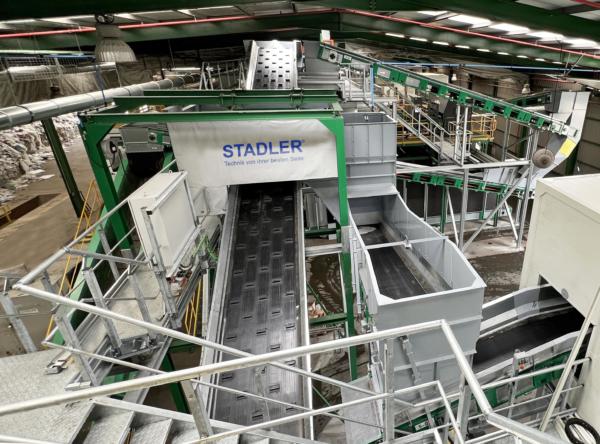
STADLER Selecciona S.L.U. (a subsidiary STADLER Anlagenbau GmbH) has designed and installed a light packaging plant for Valorsul to increase capacity and simplify operation at its Centro de Triagem do Oeste waste treatment facility in Cadaval, in the Greater Lisbon District of Portugal.
Valorsul, a leading company in the environmental sector, handles the processing of around 850,000 tons of municipal waste produced every year in 19 municipalities in Greater Lisbon and the Western Region. The company selected STADLER for the design and installation of a new sorting plant at its Centro de Triagem do Oeste, one of the two light packaging treatment facilities it operates. With this project, Valorsul aimed to increase throughput capacity of the facility while maintaining the high purity of its outputs, as well as simplifying its operation. António Afonso, Recycling Plant Manager at Valorsul explains: “We chose STADLER because of the quality and detail of the studies they presented. Also, the visits we made to various facilities designed by STADLER allowed us to ascertain the quality of the equipment and of its assembly.”
New plant delivers increased throughput capacity with high purity output
The process begins with the incoming waste being fed into a bulky items sorting cabin and bag opener before going through two STADLER STT2000 ballistic separators that separate the flexible and 3D materials. Film recovery from the flexible output is improved with the use of a new aspiration system and STT2000 ballistic separators with forced ventilation. Metals are recovered from the 3D materials from ballistic separation with new electromagnet and eddy current separators, and sorted into ferrous and non-ferrous metals, while optical sorters recover PET bottles, HDPE, Tetra Pak and a Plastic Mix. An optical sorter from the original plant is used to conduct an automatic quality control of the PET, HDPE and Tetra Pak fractions.
“To increase the facility’s capacity while maintaining the high quality of the output, we have replaced the one ballistic separator in the original plant with two STT2000 ballistic separators and we have installed larger capacity optical sorters featuring the latest technology. We have also included two new sorting cabins to simplify manual sorting and quality control,” says Carlos Manchado Atienza, STADLER International Sales Director.
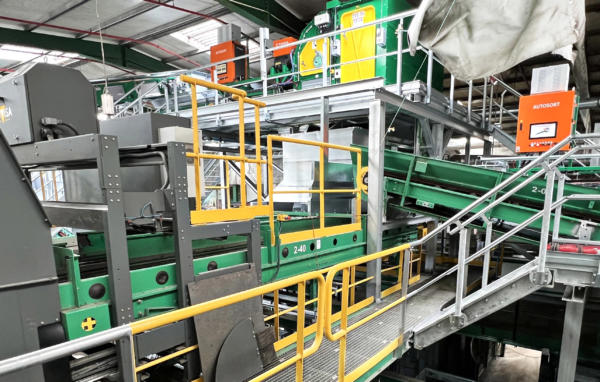
Designed for simpler operation
Simplifying the plant’s operation was another important requirement from Valorsul. To address this demand, STADLER designed the layout to allow for better access to critical equipment. It also significantly simplified the product baling process by integrating the metal baler into the STADLER support structure, so that bales fall directly into an open box container, and by using automatic bunkers for easier storage. This approach significantly facilitates the recovery of high-quality output.
Óscar Horcajada Torres, STADLER Selecciona Project Manager, says: “For example, in the ferrous metals baling process, we use a smaller bunker which, in coordination with the elevated baler and the new quality control cabin, greatly simplify the recovery of high-quality ferrous metals.”
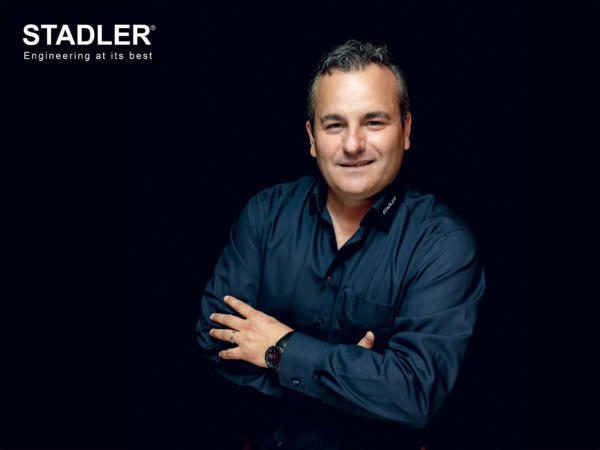
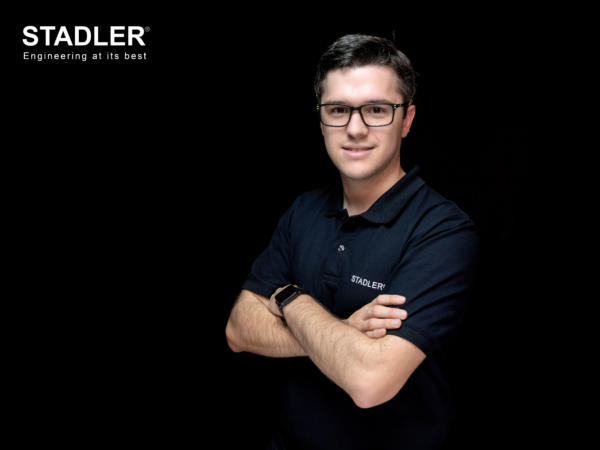
Detailed analysis and careful preparation for a successful outcome
The new design needed to fit with the original plant’s feeding and baling area, which were retained: “To ensure the seamless integration with the existing structure and equipment, we collected as many drawings and documentation of the original facility as we could,” explains Óscar Horcajada Torres. “Also, plant modelling with a 3D scanner was very important. The excellent communication with the team at Valorsul was essential to the successful outcome of the project.”
António Afonso adds: “During the design phase, I would like to highlight the great willingness and collaboration of the STADLER team in meeting all of Valorsul’s requirements, demonstrating a high level of experience, knowledge and competence that made it possible to achieve a high-quality project. They achieved a perfect integration of the new equipment with the existing machines, achieving an organized, fluid sorting line with no operational constraints, and with accessibility to all equipment and circulation paths along the entire sorting line.”
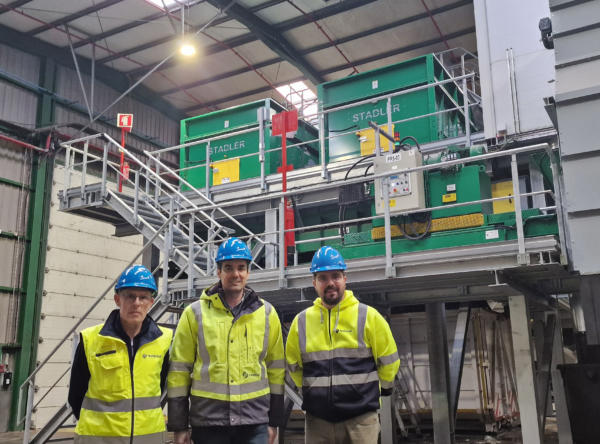
Careful planning, flexibility and effective communication for delivery in record time
The project presented a particular challenge as the original plant had to be disassembled with extreme care in order to safeguard the existing equipment that would be used in the new design. STADLER also had to work within an important time constraint, as space for storing the waste coming from Valorsul’s collection during the works was limited. “Careful planning and our well-prepared assembly team were crucial, as was the good coordination with the Valorsul team,” says Óscar Horcajada Torres.
STADLER completed the disassembly of the existing plant and assembly of the new one in a record time of 7 weeks, and the new facility was inaugurated in November 2023 to the great satisfaction of Valorsul: “During the assembly phase, the STADLER team stood out for its high level of experience, availability and compliance with safety rules, enabling the project to be carried out safely, on schedule and without delays,” concludes António Afonso.